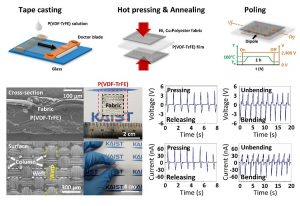
It is based on the ferroelectric polymer poly(vinylidene fluoride-co-trifluoroethylene), built into a heterostructure with two conductive fabrics (diagram right), which can then be applied to fabric by a similar hot-pressing process to that used to attach graphics to T-shirts – taking two to three minutes on polyester.
The patch has been analysed electrically and theoretically, as well as physically using a surface and interfacial cutting analysis system (SAICAS – image left).
“This study could enable the commercialisation of durable wearable devices based on the analysis of their interfacial adhesion strength,” said Professor Seungbum Hong. “Our study lays a foundation for the manufacturing process and analysis of other devices using fabrics and polymers. We look forward to fabric-based wearable electronics hitting the market very soon.”
The polymer used here offers a piezoelectric modulus of −32.0pC/N, and the layers of the harvester stick together with a strength of 22N/cm.
Strong bonding comes from the temperature at which the patch is processed.
“The polymer film is pressed onto a fabric below its crystallization temperature and transforms into an amorphous state,” according to KAIST. “In this state, it compactly attaches to the concave surface of the fabric and infiltrates into the gaps between the transverse wefts and longitudinal warps. These features result in high interfacial adhesion strength.”