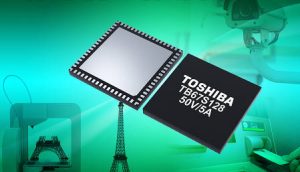
TB67S128FTG, as it is to be known, also supports full, half, quarter, 1/8, 1/16, 1/32 and 1/64 step operation – micro-stepping is by PWM, using sine-wave derived on-off ratios – output chopping frequency can be adjusted by external resistance and capacitor.
Power dissipation is minimised using low-output resistance (0.25Ω) p and n-channel mosfet output bridge transistors – integrated using a BiCD process – allowing it to fit in a 9 x 9 x 0.9mm 0.5mm pitch QFN64.
Several Toshiba technologies are included to improve motor driving (spot the re-purposed acronyms) :
- AGC (active gain control) optimises drive current to suit required torque – preventing stalls and saving power.
- ACDS (advanced current detection system) controls motor current without a sense resistor – although an external sense resistor can also be used.
- ADMD (advanced dynamic mixed decay) automatically optimises switching control of ‘fast decay’ and ‘slow decay’ modes to secure high speed rotation.
- SMD (selectable mixed decay) sets the ideal, according to Toshiba, current control according to the characteristics of the motor to be used.
Applications are expected in 3D printers, surveillance cameras, electric actuators, banking terminals (ATMs), office equipment, fax machines, amusement machines and home appliances.
“The TB67S128FTG reduces noise and vibration by delivering 128 micro-stepping compared to the 32 steps of other drive ICs,” claimed the firm.
Protections include: thermal shut-down, over-current and output open-circuit detection. In the event of a fault being detected, error flags are set for the host MCU.
A built-in Vcc regulator provides power for the internal circuit.