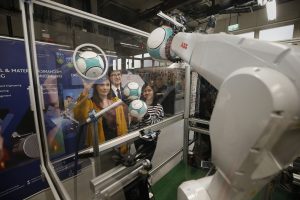
Engineering students (from left) Sarah Brady, Anthony Newell and Axieh Bagasol. Photograph Nick Bradshaw
The football factory demo was popular at exhibitions around Europe, where it was used to showcase the principles of intelligent, automated production equipment, with self-diagnostic and adaptive capabilities. It takes regulation-sized footballs and tests them for parameters such as weight, air-pressure, bounce height and roundness. An industrial robot handles the footballs and the demo’s assembly line uses adaptive manufacturing technologies, including Maxim’s Go-IO industrial IoT (IIoT) reference design. An iPad app wirelessly controls the assembly line and can be configured to identify, test and sort different sized footballs, adjusting sensor calibration and the robotic software to accommodate the various sizes.
The Go-IO IIoT reference design consists of the company’s industrial automation chipset made up of 12 ICs, 17 I/Os, supporting multiple digital I/O configurations, a four-channel I/O-Link master to interface to both analogue and digital sensors, and a 25Mbps isolated RS-485 communications channel for uploading data to the cloud.
“This factory gives . . . students [and] . . . staff, particularly those from mechanical, electrical and control engineering and computer science, the opportunity to experiment and learn how to design future production facilities, which are highly connected, increasingly intelligent and even self-aware,” said Professor Denis Dowling, UCD School of Mechanical and Materials Engineering and Director of I-Form, the SFI Advanced Manufacturing Research Centre.
Last seen at electronica in Munich last month, the football factory will not be resting in its new home: “We are very happy that we can now pass the factory on to good hands to help educate a new generation of students and prepare them for the technological challenges of the future,” said Jeff DeAngelis, managing director, Industrial & Healthcare Business Unit, Maxim Integrated.