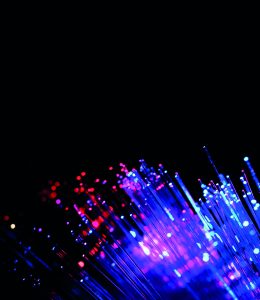
Fiber optics
Whether used for lighting, sensing and safety applications or for autonomous driving capabilities, the vehicles of tomorrow will require vast amounts of real-time data from 5G and emerging 10G networks. It is therefore key to incorporate high-speed, high-volume fibre optic connected PCBs into vehicle designs to manage the flow of data.
Fibre optics are connected to PCBs through fibre optic transceivers. These small intricate devices are fixed onto the PCBs, making it possible for optical signals to turn into electrical pulses.
Fibre optic components on PCBs offer superior bandwidth, higher speed and greater durability. They are lighter than traditional PCB components, which is an important benefit for electric-powered vehicles. In addition, fibre optic power requirements are minimal, and the risk of electromagnetic interference is less than PCBs, helping to ensure performance and longevity.
Contamination risks
Automotive manufacturers must carefully manage the production of fibre optic-connected PCBs to ensure they work reliably. Contamination is one of the leading causes of fibre optic failure. Removing microscopic dust particles, salt and fingerprint oils is essential as these contaminants can interfere with the light path moving through the fibre and the transceiver end faces (Figure 1). It can change the angle of the light or block the signal altogether.
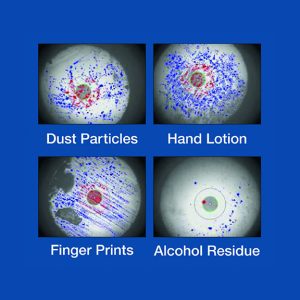
Figure 1: Examples of contaminated end faces
It is essential that transceiver connections are thoroughly cleaned during installation or maintenance. The products and processes to clean fibre optics, however, are very different from those used to clean PCBs. Fibre optic connections must be treated with extra care using specially engineered fibre optic cleaning tools and fluids.
How to clean fibre connections
When cleaning fibre, always use the rule of ‘inspect, clean, inspect’. First, inspect the connectors to identify the level of contamination using a specialised 200x or 400x digital inspection scope. This shows the location and level of contamination that may affect the signal prior to installation.
The wet-to-dry method is recommended to successfully clean fibre end faces (Figure 2). Apply a high-purity fibre cleaning fluid onto a lint-free wipe and swipe the connector from the damp area toward the dry area. If using a cleaning stick, wet it directly from the fluid dispenser before inserting it into the connector.
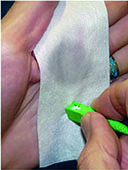
Figure 2: The wet-to-dry method is recommended to successfully clean fibre end faces
For click-to-clean tools, apply a small amount of cleaning fluid to a wipe first. Then touch the tool to the dampened area. Next, insert the tool into the connector and push the tool handle until you feel and hear it fully engage. Do not spray the cleaning fluid directly onto the connector or onto the tool itself.
Whether using a wipe, stick or click-to-clean tool, always re-inspect the connector to ensure all contamination is removed. Be sure to clean and inspect both ends of the connection after cleaning and before mating to avoid cross-contamination.
Tools of the trade
Choosing tools wisely is important when using the wet-to-dry cleaning method. The cleaning fluid should be engineered specifically for fibre optic cleaning (Figure 3). It must be high-purity, non-flammable and fast drying to quickly dissipate any static charge. The fluid should come in a sealed container to prevent the absorption of airborne contaminants, such as moisture and dust particles, which can degrade the cleaning process.
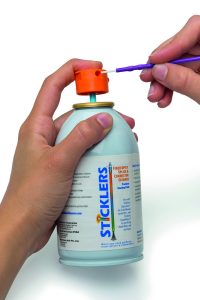
Figure 3: Fibre cleaning fluid should be engineered specifically for fibre optics
Wipes should be optical-grade to prevent lint contamination or static charge generation. These too should be packaged in sealed containers to keep them pure and clean before use.
A cleaning stick should be engineered specifically to match the configuration and size of the connector and be non-linting for optimal cleaning. Use one stick per end face and rotate only in one direction to avoid cross-contamination of the end face (Figure 4).
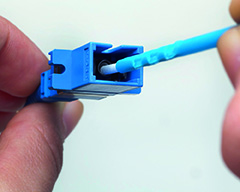
Figure 4: To clean, rotate the cleaning stick in one direction to avoid cross-contaminating the end face
Mechanical click-to-clean tools should be kept clean until ready to use by leaving the protective cap on the tool.
Cleaning for future success
Fibre optic-connected PCBs are helping to increase vehicle function and safety. Ensuring reliability is critical and it is important for PCB fabricators to understand how to clean their fibre optic connectors for consistent reliability and performance. To ensure quality cleaning, use specialised fibre optic cleaning tools and remember to inspect, clean, inspect.