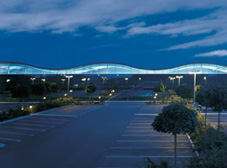
A new robotics development centre at the consumer manufacturer’s facility at Malmesbury in Wiltshire is planned to open this year.
The level of electronics and software design necessary for products such as the Dyson 360 Eye robotic cleaner, which was unveiled in Japan last year, is substantial and this is expected to increase further with future products.
Dyson has committed a £1.5bn investment to future technology development, including £1bn for the research and development of new product technologies.
It is developing four new portfolios of technology, and has plans to launch 100 new products around the world in the next four years.
Recruitment is already underway for engineers to expand the company’s electronic research in areas such as robotics, vision, machine learning, IoT and connectivity, sensors, actuator technologies and acoustic technologies.
Claudio Zizzo, global head of electronics at Dyson, is tasked with building an electronics design capability, recruit engineers, establish new laboratories, define processes and tools, to support manufacturer’s product plans.
“In the past people did not think about Dyson as a high tech electronics company, but we are changing this perception,” said Zizzo.
Dyson has recruited 60 electronics development engineers in the UK in the last 12 months and Zizzo says there are plans recruit another 70 plus engineers this year.
The company is looking for graduate engineers as well as senior and principal engineers with project experience.
Hardware design activities at Dyson are wide-ranging including high speed signal processing, motor and actuator control, sensors, RF circuit design and system level design and integration.
“The challenges our designers are tackling include real-time video processing from the 360 Eye robot’s adaptive imagers to enable navigation and localisation in different environments using complex non-deterministic algorithms,” said Zizzo.
Optimising energy use is an important element of the electronic systems design. “This means optimising energy use in the operation of the motors, but also giving the system the intelligence to chart the optimum paths for cleaning the floor,” said Zizzo.
The robot cleaner’s intelligence comes from its many microprocessors executing advanced probabilistic and heuristic algorithms and its ‘eyes’ come from tens of sensors including a 360 degree camera. The body of the robot measures 242 × 230mm and is only 120mm high so that a big design challenge is to fit the electronics into the limited space of the robot considering that most of the space available is taken by the vacuum cleaner system driven by a digital motor, the traction system, the floor brush bar system and the battery pack.
Embedded software design, complex and algorithmic design and connectivity are other growing activities at Dyson.
According to Zizzo, this ranges from firmware for controlling in real time actuators and sensor systems to higher level control algorithm design. There is also a team responsible for IoT, Wi-Fi and software app development.
“There is really an electronics revolution taking place here,” said Zizzo.
The company’s “campus-like” work environment is a big feature of how the development teams at Dyson operate.
According to Zizzo, the average age of the work force is 27 years.
“It is a vibrant and dynamic working environment which is more similar to a university campus than a company,” said Zizzo.
“People are given the opportunity to be creative and this is reflected in the way the engineering department operates. It is really an exciting time to work at Dyson,” said Zizzo.