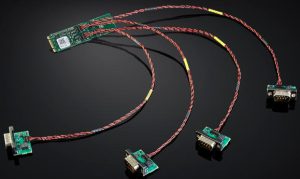
Called ‘M.2 PCIe 4xCAN’ (and also 01333-9), it works with PCI Express M.2 slots with B or M keying.
It has a main 22 x 80 x 2mm M.2 main board, and four smaller satellite boards (see images) that carry the CAN transceivers and their connectors “allowing them to be located closer to the CAN networks themselves”, according to the company. “This layout maximises signal speed and integrity, making it ideally suited for CAN FD.”
Cabling is 300mm long, and each CAN channel is individually galvanically isolated.
Time stamp resolution of is 1μs and up to 20,000message/s/channel is available. Silent mode, and error frame detection and generation are among the features implemented.
Multiple boards can be combined to provide 12 or more CAN channels. Operation is over -40 to 85°C.
An SDK (software development kit) called CANlib, which supports Windows and Linux, is available for the hardware.
Applications are foreseen in motor control for mobile robots, automated driving simulation black boxes, medical automation data acquisition, fleet management or industrial system monitoring.
Find more on the M.2 PCIe 4xCAN web page
Kvaser has R&D and production in Mölndal, near Gothenberg, Sweden, and regional offices in California, Shanghai and Hong Kong. It makes CAN interfaces, and offers custom design service for OEMs and ODMs.